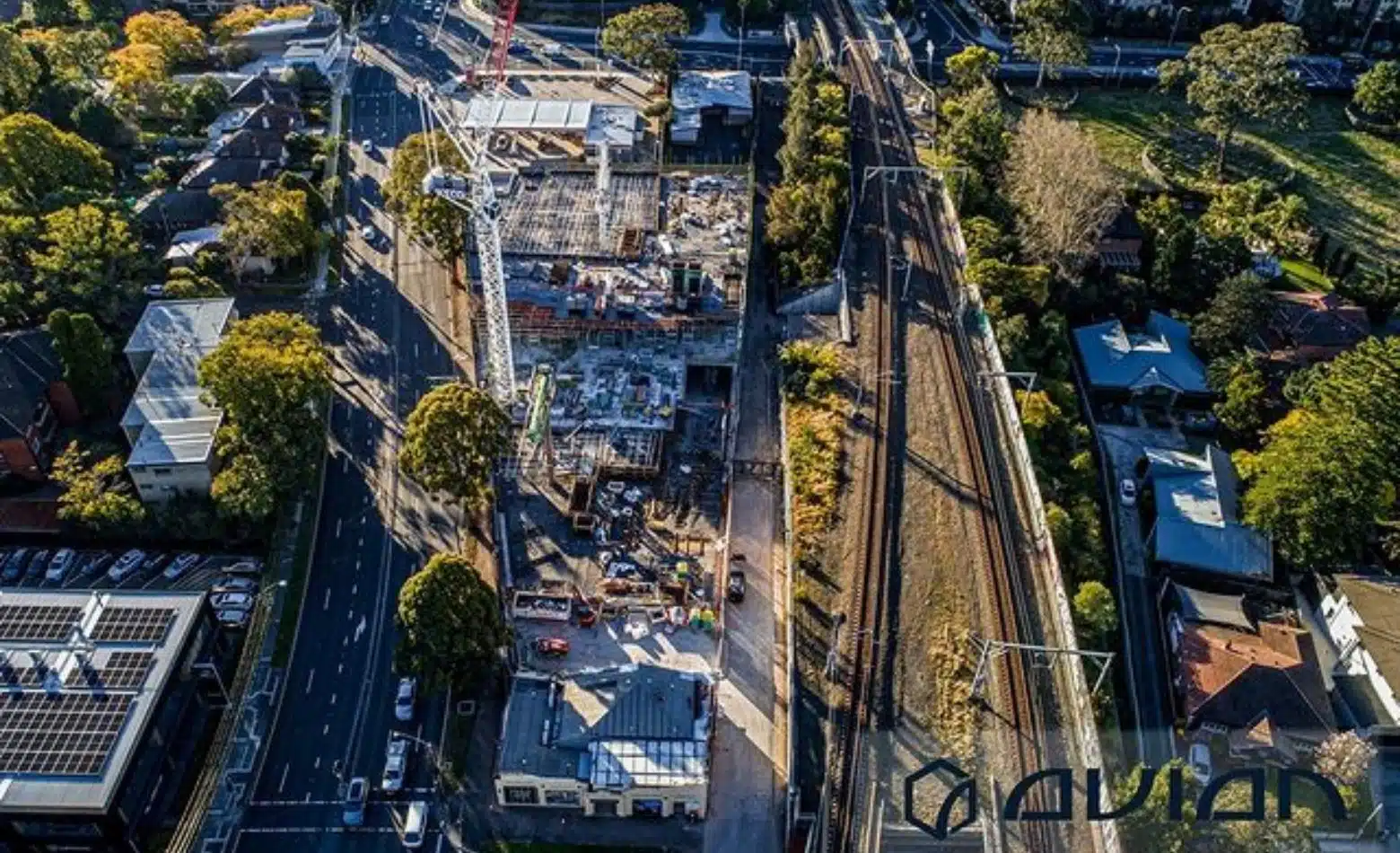
Construction sites are a dynamic and busy operation and project managers and builders need to constantly check and recheck site operations and contractors to ensure that everything is on schedule and on time. As you would likely agree, it’s probably easier said than done!
That’s why, new technologies in drone surveying are increasing in popularity and wider adoption on both medium to large construction projects. However, it’s important to understand how credible and accurate the site measurements and calculations are compared to traditional land surveying methods
Over the years, we have come across some common drone surveying mistakes that could hamper your project.
Let us see what these surveying errors are and the best ways we can avoid them.
Table of Contents
One major problem with the current drone ‘surveying’ services is: drone operators fail to understand the surveying principles needed when capturing site data. Surveying as a practice has evolved over 4,000 years (since 3000BC) so arguably surveyors have been measuring, observing and documenting land topography for a lot longer than drones have been around!
You will find a lot of drone services in Melbourne such as drone photography that will assist with capturing images and drone surveying and mapping services for creating maps or models. But with no guarantee or certainty of their data accuracy, methodology or equipment performance that can be relied on for making critical project decisions.
Most drone operators rely on drone positioning systems (GPS), without any checks for production errors, or rely on photogrammetry and GCPs to make it ‘right’.
In this article, I will be covering four main drone surveying mistakes and common ways to avoid them.
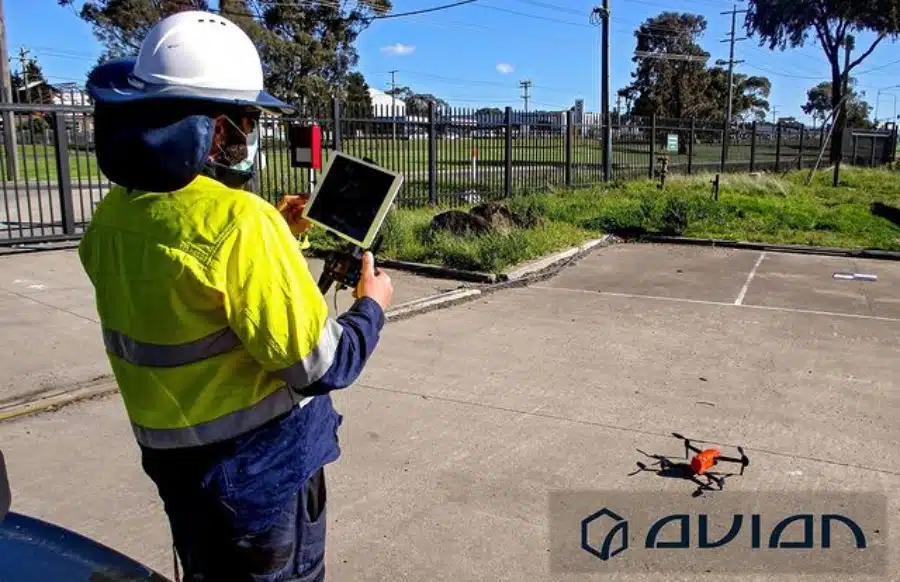
Not using any ground control points (GCPs)
GCPs or ground control points are basically survey marks, visible from the aerial images, of targeted locations on the survey site that can be used as reference points when processing the data into 2D maps or 3D models.
These GCPs are essential for the generated maps/models to be geo-referenced to be correctly positioned within a real world location and to align with other GiS applications.
One of the biggest drone surveying mistakes you can commit is not using GCPs during an aerial survey.
By using GCPs, the processed maps and models will be accurate in relation to the GCPs on ground but without GCPs, drones capture images within a 5-meter radius. And while the relative error of dimensions is less horizontally (x,y axis), there is a significant difference when you check the vertical (z axis) accuracy of the survey.
The accuracy of the data, without GCPs, when compared to the GPS locations on the ground gets significantly worse when you measure vertically. The difference can be upto 15m from the actual location!
How to Avoid It
Using GCPs or some sort of a survey control, you can determine the exact location of the site dimensions when processing the drone images captured from the air.
In simple terms, GCPs ensure that the latitudes and longitudes on the map correspond with real-world GPS coordinates on the ground.
GCPs are useful for projects that depend heavily on precision and accuracy or that require high levels of global accuracy.
In construction projects, GCPs are often used for inspection, terrain mapping, stockpile management, site calculations, tracking on-site productivity etc.
We use a minimum of 5-6 GCPs throughout the site area, depending on the size and scope of your project.
Not spreading the GCPs strategically.
Service providers (both surveyors and drone operators) often conduct a desktop review (virtual site visit) before they come up with a cost estimate or proposal. This site visit is basically an inspection of the site topography, neighboring features, site perimeters, vegetation etc.
Another common drone surveying mistake is when drone cameras aren’t able to see through vegetation (trees, short grass, bushes).
So if there is vegetation in the target area this can cause problems when measuring the natural surface or actual topographical detail.
A huge red flag in drone surveying is when your service provider doesn’t verify the site physically, thereby not covering the target area or the surrounding topographical features in their survey.
A desktop analysis/site visit helps the surveyor also determine where and how the GCPs will be placed around the property to ensure maximum coverage and ensure uniform geo-referencing to improve successful data processing.
If there are no ground control points on the edges or sections of the site area, the software doesn’t have any insight to geo-rectify those regions. Also, without any checkpoints, you cannot really ensure survey data accuracy.
And if there is a section on site with thick tree coverage, vegetation or water bodies, the photogrammetry software won’t be able to find matches within the images due to the featureless terrain. As a result, the point cloud in those areas will be black or contain holes.
How to Avoid It
A rule of thumb we follow when it comes to using GCPs- always use too much instead of too little GCPs. It is hard to add more ground control points rather than discard a few extra ones during processing.
The placement and spacing of the GCPs are of utmost importance. Also, depending on the area covered, the number of GCPs used will vary from project to project. For example a long road corridor requires GCPs in a zig zag arrangement as compared to a rectangle site area where GCPs are scattered within the rectangle.
Spread the points evenly across the site and make sure you include site geographical features such as tree lines, elevations, ground depressions etc.
Wrong direction during drone flight.
Believe it or not, this drone surveying mistake is more common than you’d think. When the difference in survey measurements are more than 0.1ft, it is highly probable that something has gone wrong during the drone surveying.
A main reasons behind these errors can be low satellite coverage or inaccurate altitude recorded from the drone itself. This can happen when the drone’s compass is not calibrated properly or the internal barometer has been affected by wind or humidity. As a result, drone operators may experience the flight direction and altitude being abnormal during flight and incorrectly recorded.
Data discrepancies may also occur if the GCPs have been physically moved during the operation.
How to Avoid It
Ensure that the drone operator or surveyor conducts a site inspection and confirms a proposed methodology for the job scope beforehand to ensure that the GCPs are properly placed throughout the site and the data acquisition goes according to plan.
Also, it is important that your drone operator or surveyor proposes the CRS (Coordinate Reference System) and datum to be used for the survey to ensure the results are compatible with other GiS, surveying or engineering plans.
Other than that, it is always best practice to plan for localised weather conditions of the area before you begin drone surveying operations. This is to ensure the wind, sun and rain and at acceptable levels to conduct aerial surveying operations. Too much of either can cause significant errors in the images and resultant data that is produced.
Poor flight plan and camera settings that yield blurry footage.
Ever noticed a few blurry and distorted patches in the imagery in the middle of a footage? This is because the drone camera settings are not ideal.
The blurry patches often appear outside the line of the flight path, especially on buildings and the edges of the flight boundary, where the drone is changing direction.
Distortion also occurs when the drone is flown very high. This reduces the ground sampling distance and subsequent accuracy.
How to Avoid It
First, ensure that the flight boundary is at least 10-15% larger than the target area that you’re interested in mapping. At the boundary the number of images used for matching is lower, so you need extra space to guarantee good results.
Secondly, ensure that you get the right image overlap. We generally fly with at least 75/70 to ensure we can get enough data to model each site area accurately. But this ratio is increased with areas of uniformity such as large forested areas, water or large commercial roofing.
If the purpose is 3D modeling, in addition the camera angle should be adjusted to 15-30% and multiple flight paths are required to ensure adequate capture of vertical surfaces.
The Bottom Line
Drone surveying is an indispensable part of any AEC project. And the simplest of mistakes can cost you quite heavily in delays, revisits and errors in miscalculations and estimates. It pays to ensure the data is both accurate and precise to ensure the utmost confidence in the results.
The points mentioned above are but just of the things that can go wrong with a drone survey.
At Avian Australia, our drone operators and surveyors are trained, experienced and certified by CASA to handle all kinds of operations. We have a sharp eye for detail and proven workflows that leaves no room for errors, ensuring that your project is completed efficiently, accurately and within the deadline.
Please feel free to reach out to our team at Avian to help you with your drone surveying services, drone mapping or terrain modelling requirements and see the difference reliable results can make to your projects.