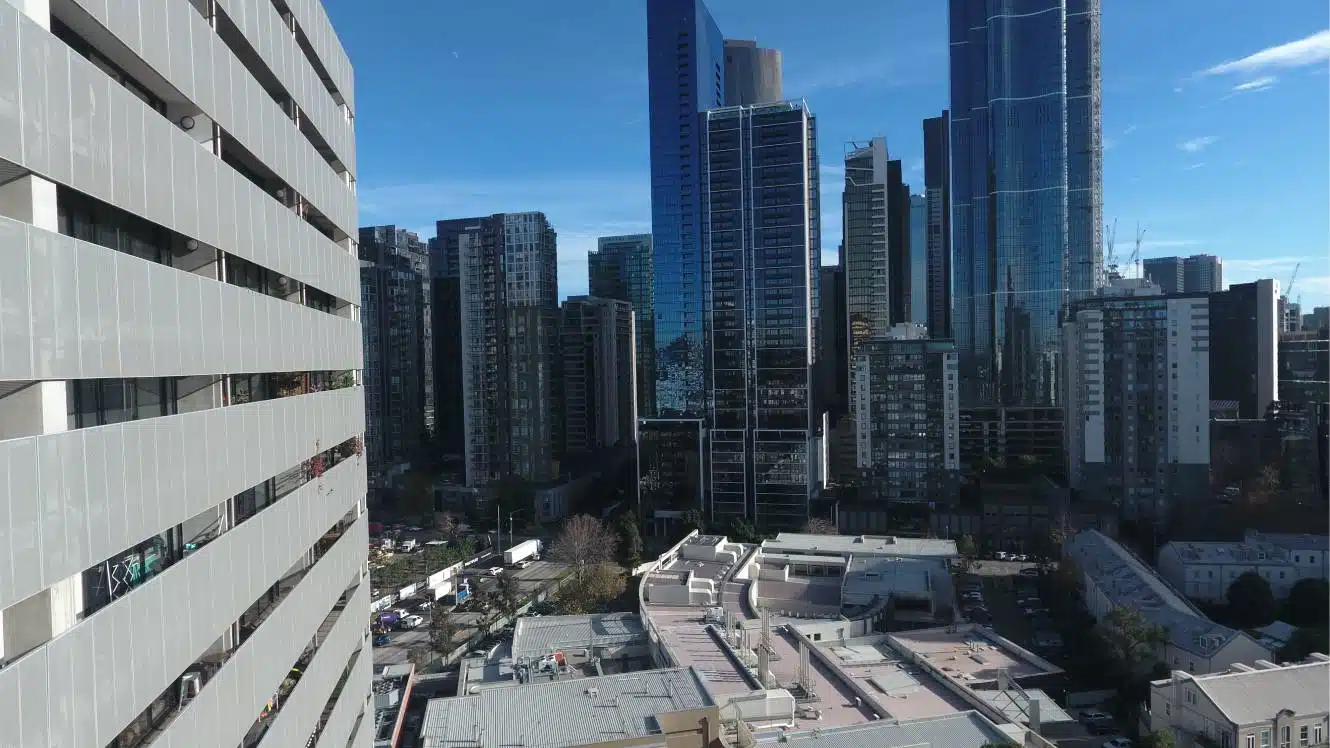
Revolutionizing High-Rise Building Facade Inspections: Avian Australia's Drone-Powered Success Story
Introduction
In this case study, we will explore how Avian Australia, a leading digital imaging and reality-capture company, collaborated with Commercial Building Inspectors to revolutionize high-rise building facade inspections. Avian Australia’s innovative use of drone technology has transformed the traditional, time-consuming, and resource-intensive inspection process into a faster and safer operation.
Client Background
Our client, a prominent player in the commercial building inspection industry, faced a common challenge in their line of work. Traditional high-rise building facade inspections required the laborious use of rope access workers, involving significant time, resources, and risks. Avian Australia stepped in with a groundbreaking solution to modernize this critical aspect of building maintenance and safety.
Problem Statement
The problem was clear: conducting thorough inspections of high-rise building facades using rope access workers was not only time-consuming but also posed safety concerns. The need for a more efficient and safer method of inspection was evident.
Avian Australia’s Solution
Avian Australia’s solution was to leverage the power of unmanned aerial vehicles (UAVs or drones) to conduct high-rise building facade inspections. Their solution included:
– Providing fully licensed, insured, and experienced UAV inspection services across Australia.
– Deploying professional-grade quadcopters equipped with advanced safety features, including parachutes and propeller guards.
– Implementing obstacle avoidance sensors to maintain a safe distance from the building facade, ensuring optimal image capture and inspection efficiency.
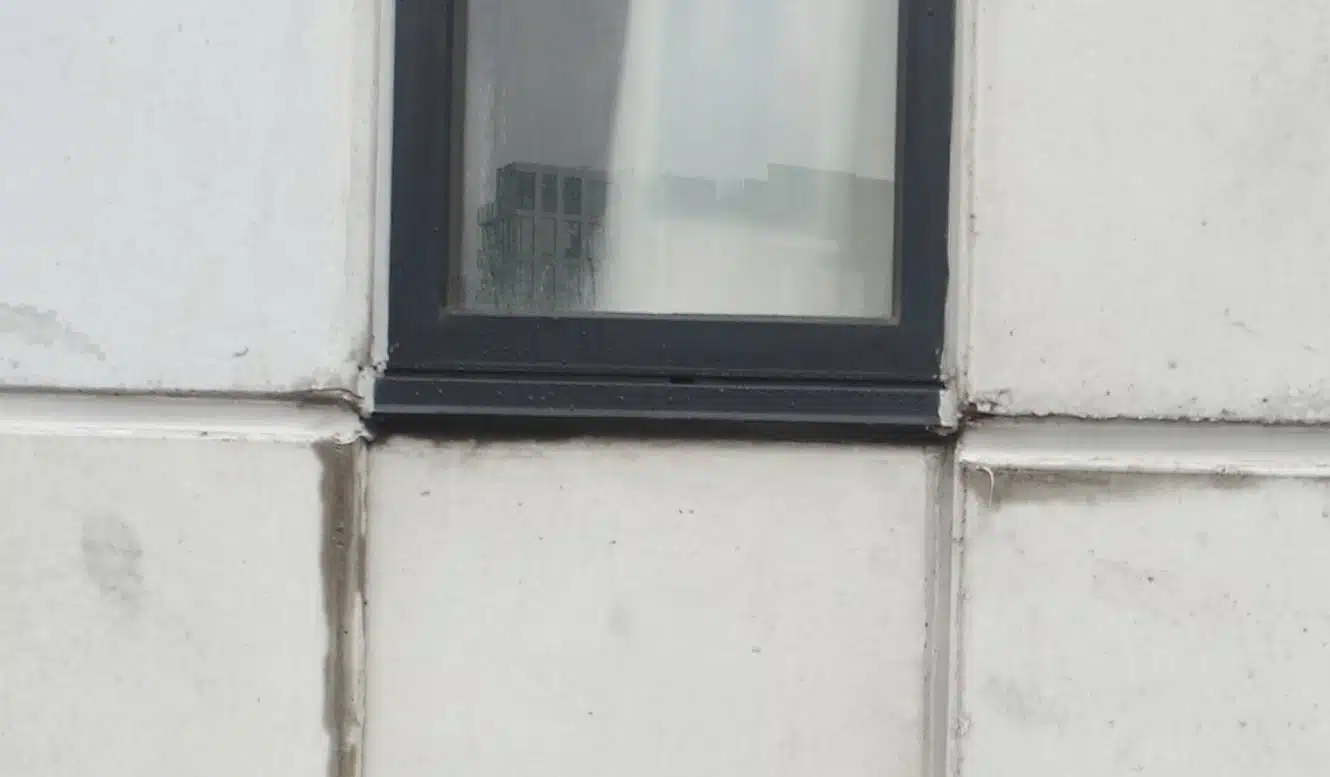
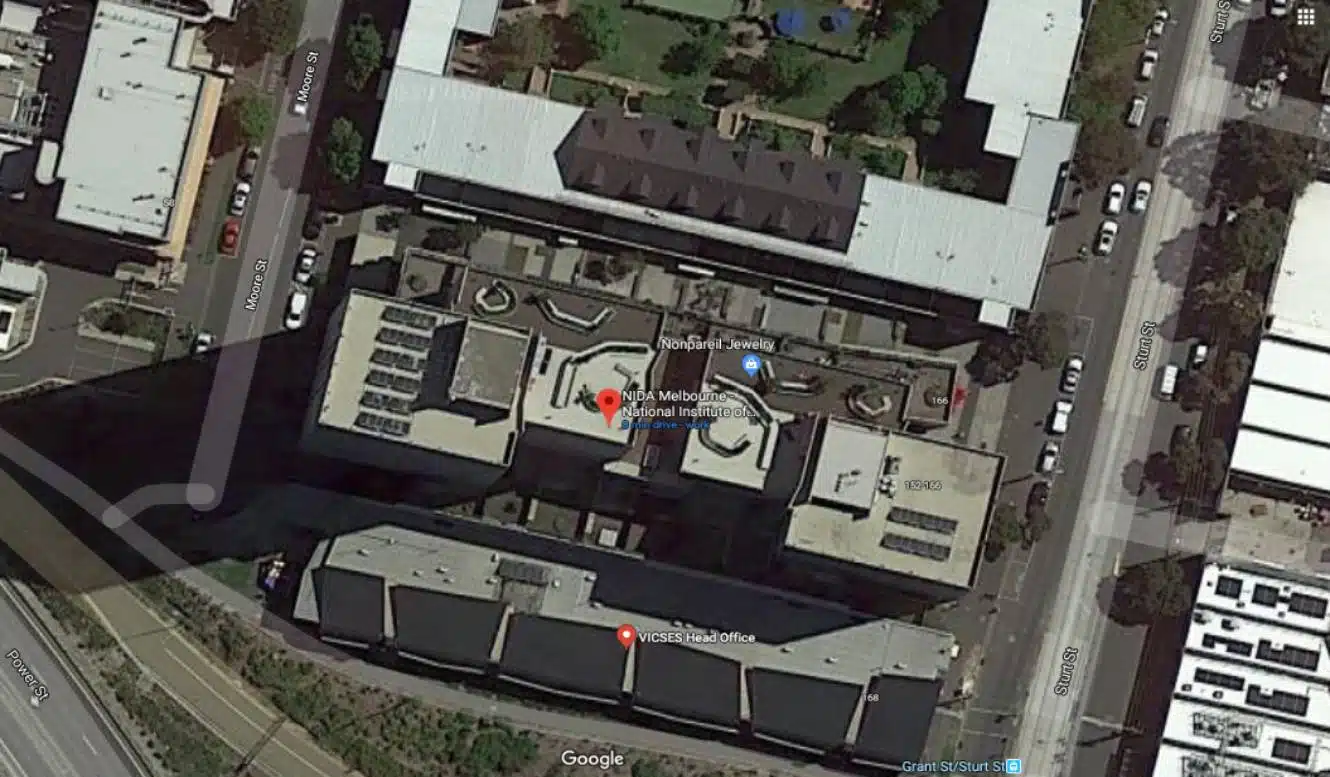
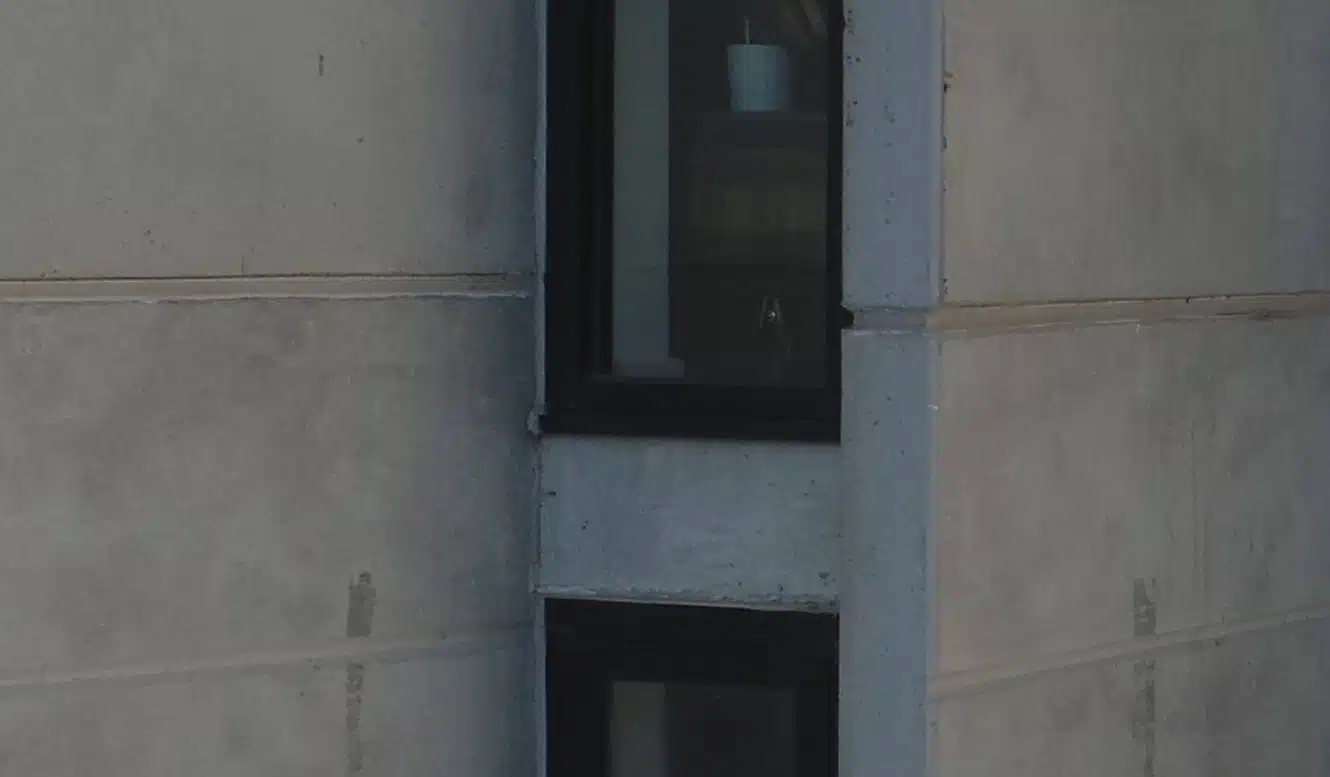
Implementation
Avian Australia executed their solution efficiently and safely. They conducted inspections of a complex comprising five adjoining buildings, each with multiple facades, ranging from 7 to 25 floors. A building engineer oversaw the process, monitoring live HD video streaming directly from the drone. The drone captured photographs and videos of every meter of the building, providing valuable data for inspection reporting.
Avian Australia deployed a professional-grade quadcopter with a 20MP camera fitted with key safety features of a parachute and propeller guards to minimise the risk profile of the operation. Pedestrian management regulations were deployed along the walkways and main entrance to the building along with safety signage and equipment.
Results
The results of Avian Australia’s innovative approach were remarkable:
✓ The entire complex’s inspection was completed in just 1.5 days, with a swift file handover within 5 business days.
✓ A total of 1,576 images were categorized and indexed systematically, enhancing ease of reference.
✓ The use of obstacle avoidance sensors allowed for consistent image capture, with each square meter documented in 3-4 images. This improved image clarity and expedited the desktop review and inspection process.
✓ Comparatively, the traditional rope access method would have taken 12-14 days and produced less clear images due to close proximity to the facade.
Choosing the right Laser Scanning Service
At Avian Australia, we offer a range of laser scanning services tailored to meet the specific needs of architects and construction managers. When choosing the right package, consider the scope of your project, the level of detail required, and your budget. Contact us today to discuss your project and receive a customised quote.
Avian Australia Commitment
Avian Australia’s collaboration with Commercial Building Inspectors showcases the transformative potential of drone technology in the field of building inspections. By replacing traditional methods with drones, they have not only increased efficiency but also enhanced safety and data quality. This innovative approach sets a new standard for high-rise building facade inspections, benefiting both the commercial building industry and the safety of building occupants.