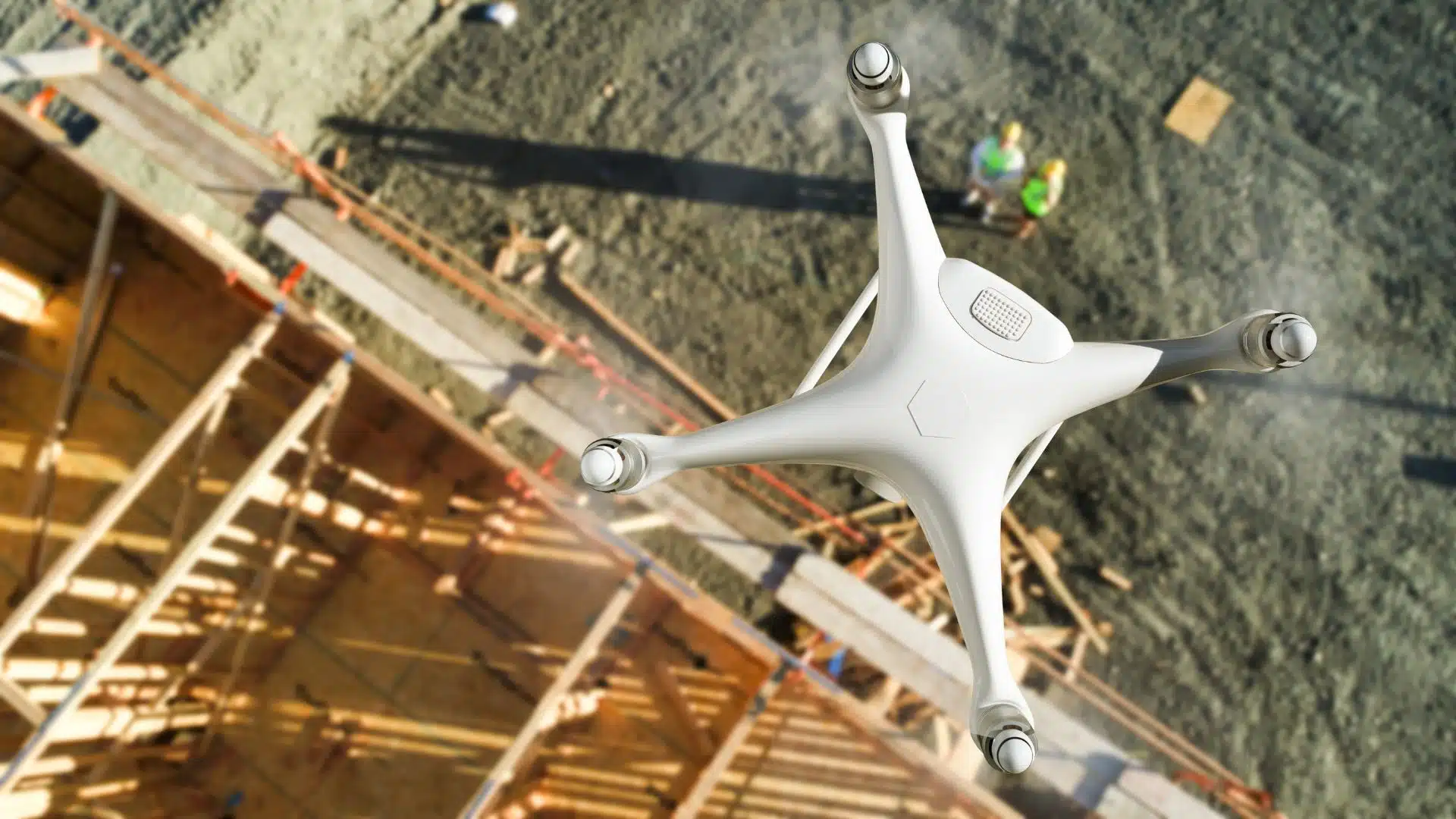
Aerial asset inspections have completely changed the way we conduct assessments of difficult to reach positions, over water, at heights or underground. The days when engineers had to setup rope access or seek numerous approvals just to get a condition assessment are long gone. Also, the manual methods of hanging from ropes or building platforms to take measurements are reducing, unless other methods are first ruled out.
Aerial inspections not only save you time and money, but also enhance your decision making in a lot of other significant ways. As aerial drone inspection experts in the engineering and construction space, we often get a lot of queries about the costs involved in aerial drone inspections.
Here are some factors that affect an aerial drone inspection operation.
Table of Contents
What is aerial asset inspection?
A best practice preventative maintenance plan must include the scope for aerial asset inspections. This method of inspection helps engineers and technicians keep track of existing conditions such as deterioration, deformation, water penetration, leaking and other conditions of the asset.
In the past, inspectors used manual methods to track the condition of assets for maintenance and repairs. This usually involves ladders, cranes, EWPs, BMUs, scaffolding and rope access. Most of these methods involve significant approvals, permits and processes to minimise risks and avoid injury. However, these methods can be a lengthy and cumbersome process and often prone to delays and additional, avoidable costs.
These days, aerial asset inspections using drones and suspension cameras have increasingly been the choice among AEC professionals. With aerial drone inspections, you get better insights, data accuracy and in-depth details on the asset in real-time.
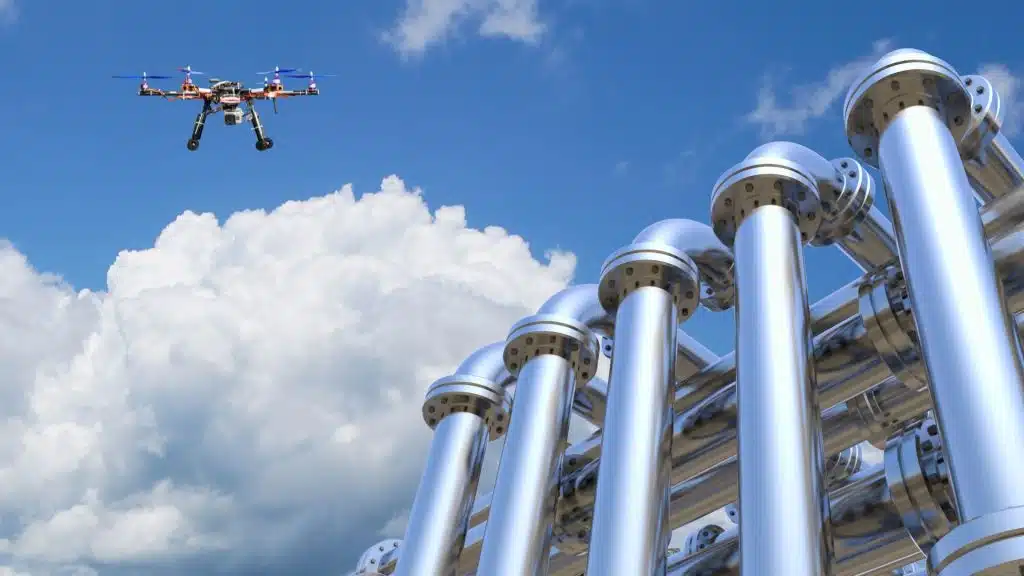
The need for drones in asset inspections
Inspecting a building, bridge, tower or similar asset is not a straightforward or simple job. It requires a lot of careful planning, logistics and calculations. Using drones in aerial asset inspection process is no different as we need to ensure the right level of detail and
data is captured using the right equipment, processes and approvals. The size, aspect, location and level of detail are all important factors that can alter the cost of an aerial drone inspection operation.
The traditional inspection methods using ropes, cranes or platforms take a lot of time and resources. Plus, these often require a shutdown of the construction project or asset due to the type of at heights access required. However, using drones can make the inspection process more efficient and safe, as engineers don’t need to access or interface with the structure unless it’s absolutely necessary.
With drones, you don’t need any heavy-duty equipment or a lot of space to operate the drone as most inspections require the drone in close proximity for the optimal inspection photography. These innovative inspection cameras can be operated over any site and require only a small team to be present during the inspection.
Drones are easier to navigate around the asset and can easily reach positions that are otherwise inaccessible, without significant effort and resources. A prime example of this is high-rise building facades, telecommunications towers or road/rail bridges that need periodic conditions assessments. These assets can take a team of engineers days to weeks to manually inspect using rope access, cranes and suspension platforms. However, drones can complete the overall condition assessment within a day or two. Drone inspections have become necessary at each stage of the asset construction lifecycle.
In the pre-construction phase, drones help engineers and project teams to understand the site terrain and topography before setting up the construction program and sending project teams to site. During the construction process, drones are used to keep an eye on progress, site operations, safety compliance and even to conduct asset audits and stocktakes of materials, machinery, raw materials, site security and other assets on and around the site.
Once construction is completed drones are used for condition assessment before handover or as part of an ongoing maintenance program.
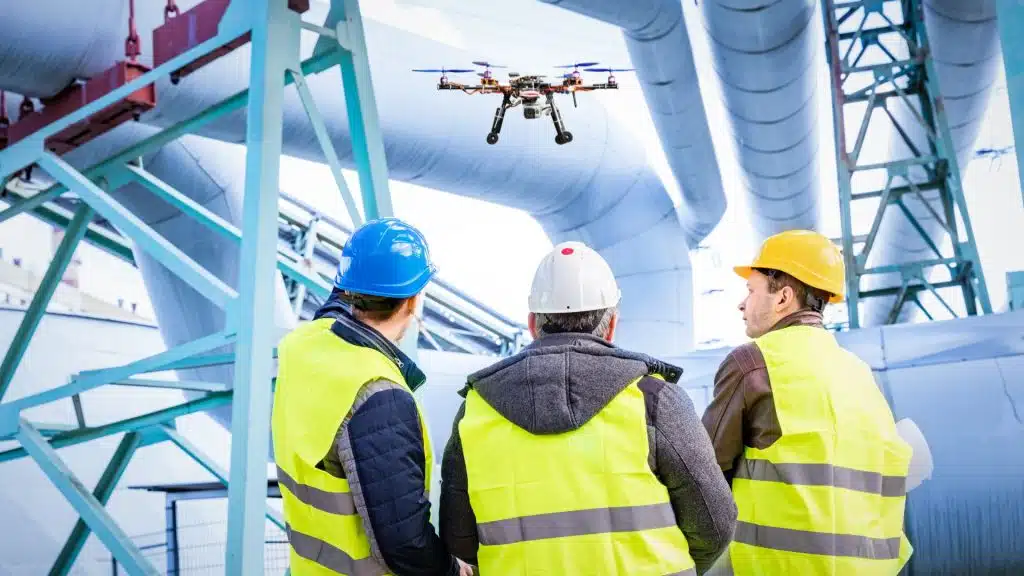
Where are aerial inspections most beneficial?
Before we continue discussing the factors impacting aerial asset inspection cost, let us first understand the various areas where drone inspections are useful for the AEC industry.
Land inspections (Pre-Build)
Drone inspections for properties are often conducted before construction begins. This can be in the form of site analysis, feasibility or context. In this survey, the drone is used for terrain mapping and surveying or to inspect the site area to check the site topography, vegetation, neighbourhood and other aspects of the property.
The drone inspections are useful for creating site survey plans, topographical models or showing a building design to potential clients using renders, photo-montage and overlays..
Building inspections
Building inspections are conducted usually for remediation, repairs or renovation projects. In this case, the engineer requires a drone inspection to check the quality of the building facades, roofing or drainage and to understand problem areas that need to be repaired or modified. This type of inspection is the most common to understand existing conditions and determine the most appropriate actions.
Building inspections are also necessary to understand the extent of reported damage due to weather and include the interiors to determine water ingress and moisture build up. Using drones for the external inspection covers the building from multiple angles and at heights without the need for people to climb on the roof, hang off the facade, or set up elevated work platforms or scaffolding. This avoids costs until the level of repairs and maintenance can be determined.
You can check out an example of building condition inspection of a high-rise residential building in Melbourne. Our methodology involves using the UAVs to traverse the external facade, floor by floor to inspect the entire building, including all facades in a matter of days. Plus our reporting is methodically categorised and indexed for reporting so that any desktop analysis is easier, targeted and more efficient.
Machinery inspections
Assets such as heavy duty machinery need regular maintenance and monitoring. Any damages to such machinery and assets can heavily impact your operations as can unplanned downtime. Regular inspections also reduce the risk of sudden breakdowns as you are aware of any faults and can address them immediately or plan downtime in advance.
Any damage to the asset is not only a financial loss but also impacts the daily operations on which the asset is required. Faulty machinery can cause malfunctions, delays and disruptions on the site and in serious situations cause fatal accidents. Regular inspections and healthy equipment maintains a healthy business and safer operations.
Check out our case study of Engineering Asset Inspection from our portfolio of past projects. In this specific project, we developed a tailored inspection process, specific for these assets using enterprise UAVs (Unmanned Aerial Vehicles) fitted with range sensors and high-magnification zoom lenses to capture close up detail of the asset from all angles.
Asset inspections (bridges, towers, buildings)
Large infrastructure and commercial assets require periodic condition monitoring and assessments to ensure the integrity of the structure and preventative maintenance can be maintained. This may involve increased frequency after weather events or in harsh environments. Using drones to assess existing conditions allows engineers and maintenance teams to plan and cost maintenance programs more effectively. The level of maintenance, materials, resources and site access can be planned with more detail as there is more information gathered about the asset, site access and the surrounding environment.
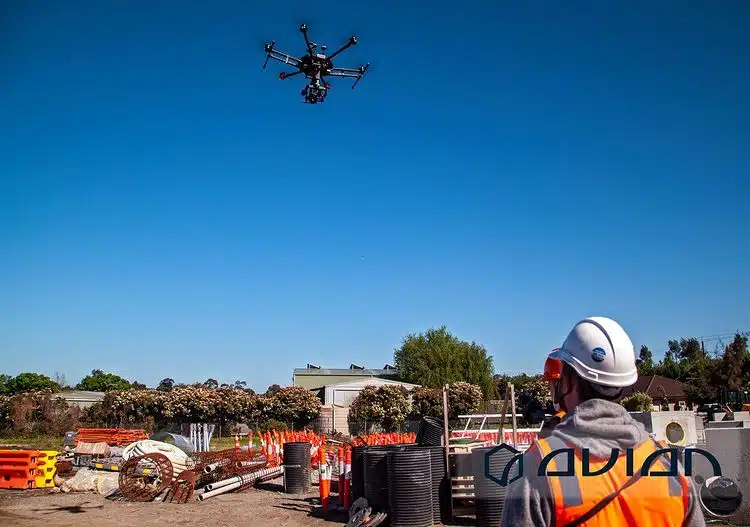
Types of aerial asset inspections in Australia
Each drone inspection has its own specific requirements and project goals. At Avian, we set up a call with the client, project team or engineer to understand these requirements and conduct our due diligence on the asset location before coming up with a proposal.
Here are a few types of asset inspections we offer.
Existing condition inspections (not just drone inspections)
Visual condition inspections are the most popular form of asset inspection and are suitable for condition monitoring all types of assets. In this inspection, our team uses drones, digital cameras or handheld sensors (thermal, moisture) to capture high resolution images and data about the existing conditions of the asset from multiple perspectives, inside and out..
Condition inspections are non-destructive, efficient and don’t need a large team of contractors to manage the inspection. All we need is a 2 person crew to conduct the inspection and we can live stream the sensor data to a screen in real-time while onsite.
With condition inspections, you can identify any faults or damages in assets such as building facades, roofing, drainage, bridge steelwork, telecommunications towers or construction sites without any unnecessary delays. This type of inspection helps inspectors and engineers to locate faults and recommend the appropriate repairs and maintenance in real-time saving you a lot of time and effort.
Visual condition inspections are conducted on a periodic basis as part of the asset maintenance program. One such example of the same is of Highway Infrastructure management.
Condition inspections usually cost between $250-$450 per hour depending on complexity, location and inspection requirements.
Thermal inspections
Thermal inspections use infra-red sensors to detect temperature differences to inspect a building or roof cavity to identify water ingress and damage. Thermal asset inspections are commonly misunderstood as there is a degree of training and expertise required to interpret the thermal camera images and to ensure correct image capture and diagnosis of the problem or extent of the damage. This type of inspection is commonly used for the inspection of solar panels, conducting rooftop inspections of commercial or residential buildings, warehouses and manufacturing plants etc.
Drone based asset inspections are conducted during the construction and ongoing maintenance and operation of assets including for insurance assessments.
Construction site inspections
Construction site inspections are required to assess the site operations, safety compliance or conduct audits of plant and machinery, site security or construction materials onsite. This is essential for companies that don’t have the ability to monitor multiple sites in geographically dispersed locations, especially when urgency and immediate information is required about site operations. These inspections can also involve road and pavement inspections to detect any damages on the road pavements, identify faults during the asset maintenance process and to get repairs and rectification works underway.
LiDAR surveys
LiDAR devices aka light detection and ranging devices are an essential aspect of large terrain mapping and modelling. Drones are mounted with LiDAR equipment to capture accurate surface information including of the as built environment. LiDAR inspections are commonly used to inspect power lines, dams, towers, pipelines, mine shafts and other inaccessible areas.
LiDAR inspections reduce on-site risks and capture survey data without the cost and complexity of covering large distances on the ground or at heights. LiDAR surveys capture site data as a point cloud that need to be processed in photogrammetry software to generate 2D and 3D feature surveys, digital terrain models and terrain maps.
LiDAR inspections usually cost between $1200-$1500 per hour.
The Bottom Line
Aerial asset inspections have changed the way we conduct investigation and assessment of assets and buildings. With modern-day technologies and tools such as drones, high magnification and thermal sensors, we can capture site data with greater accuracy, detail and efficiency.
Please contact us and book a free consultation to learn more about your unique project requirements and discover how our services and expertise can help to deliver successful project outcomes.